In accordance with the personal data protection law implemented by the European Union, we are committed to protecting your personal data and giving you control over it. By clicking "Accept All", you allow us to place cookies to enhance your experience on this website, assist us in analyzing website performance and usage, and enable us to serve related marketing content. You can manage your cookie settings below. Clicking "Confirm" means you agree with the current settings.
Bicycle Handlebar Manufacturing: Contract, Private Label, & Turnkey Explained – 4 Key Points

Table of Contents
- What are the Bicycle Handlebar Manufacturing Services?
- How Does the Bicycle Handlebar Manufacturing Process Work?
- 4 Key Points to Consider When Outsourcing Bicycle Handlebar Manufacturing
- Conclusion
The demand for high-quality bicycle components in the global market has been increasing year by year, especially with growing environmental awareness and the popularity of health-conscious lifestyles, making cycling a popular activity. Many startups are entering the bicycle market, striving to offer innovative products that meet market needs. To ensure that bicycle handlebar design and production meet expectations, many companies seek assistance from bicycle parts manufacturing partners, from design to mass production, and even help with brand planning and distribution channels.
Curious about what services are offered in bicycle handlebar manufacturing? Wondering how the process works and what key points to watch for? For those looking to create their own bicycle brand or find a new supplier, this article is a must-read!
What Are the Bicycle Handlebar Manufacturing Services?
Bicycle handlebar manufacturing services can be categorized into Contract Manufacturing, Private Label, and Turnkey solutions. Each model allows clients to outsource and mass-produce bicycle components, but the level of involvement and the scope of services vary. Here, we provide a detailed breakdown of each model and how they operate:
How to distinguish between Contract Manufacturing, Private Label, and Turnkey Solutions?
Contract Manufacturing primarily focuses on production;
Private Label offers clients rebranded products;
Turnkey Solutions provide complete design, development, and production services.
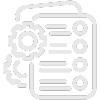
Contract Manufacturing
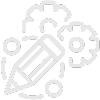
Private Label

Turnkey Solutions
Contract Manufacturing | Private Label | Turnkey Solutions | |
---|---|---|---|
Definition | Manufacturers produce products based on the client's designs and specifications. | Manufacturers offer existing products that clients sell under their own brand. | Manufacturers provide comprehensive services from design, development to production and packaging; clients receive the final product ready for sale. |
Suitable For | Companies or traders with their own product designs and specifications needing manufacturing capacity. | Companies or traders wanting to quickly launch products without investing in design and development. | Companies or traders seeking a complete solution from product development to production in a one-stop service. |
Design & R&D | Client is responsible for product design and R&D; manufacturer does not participate in design. | Manufacturer provides existing product designs; client does not participate in design. | Manufacturer provides design and R&D services, collaborating with client to develop the product. |
Branding & Trademark | Uses client's brand and trademark. | Uses client's brand and trademark, but product design is provided by manufacturer. | Can use client's brand and trademark; manufacturer may assist with branding and design. |
Production Control | Client has full control over product design and specifications. | Manufacturer controls product design; client selects existing products for private labeling. | Manufacturer is responsible for the entire production process; client involvement can vary based on needs. |
Advantages | Full control over product design and quality. Protects intellectual property. | Quick to market, saving design and development time. Reduces development costs. | One-stop service simplifies supply chain management. Manufacturer provides expertise and resources. |
Disadvantages | Bears design and R&D costs. Needs to manage production processes. | Product may lack uniqueness. Brand competitiveness may be limited. | Potentially higher costs. Less client control over design and production. |
Ideal Scenarios | Requires customized products with emphasis on differentiation. Has design and R&D capabilities. | Needs to quickly expand product line. Limited resources to invest in design and R&D. | Wants new product development but lacks internal resources. Wishes to simplify production management. |
Risks & Considerations | Requires significant investment in design and quality control. Bears risk of production delays and quality issues. | Intense market competition; product homogeneity. Brand value may be limited by product quality. | Relies on manufacturer's expertise and reliability. Must ensure intellectual property and confidentiality. |
Depth of Collaboration | Collaboration mainly at the production level. | Collaboration at branding and sales level. | Deep collaboration covering design, development, production, etc. |
How Does the Bicycle Handlebar Manufacturing Process Work?
The bicycle handlebar manufacturing process is a collaborative, precise, and iterative procedure involving multiple stages, from initial consultation to final mass production. Each phase plays a crucial role in ensuring that the final product meets the desired specifications and quality standards. Below is a comprehensive overview of the handlebar manufacturing process to help you understand how to work with a manufacturing partner effectively:
01
Initial Consultation
02
Quotation Confirmation
03
Sample Production and Testing
04
Final Sample Approval
05
Mass Production
06
Inspection and Delivery
4 Key Considerations for Outsourcing Bicycle Handlebar Manufacturing
When outsourcing bicycle handlebar manufacturing, several key factors must be considered to ensure that the final product meets quality standards and can successfully enter the market. From minimum order quantities (MOQ) to cost factors, quality consistency, and manufacturer certifications, these considerations are crucial to the success of bicycle handlebar production. Below, we discuss four essential points to evaluate before outsourcing to help you choose the right manufacturing partner.
-
Confirm the Minimum Order Quantity (MOQ)
MOQ (Minimum Order Quantity) is the smallest order size required for production. When outsourcing materials and manufacturing, extrusion suppliers typically set an MOQ. If your order doesn't meet this, you may need to pay extra setup fees, and suppliers might still refuse small orders. Therefore, confirm your order meets the MOQ before proceeding with the manufacturing agreement. -
What Factors Affect Costs?
There are many factors that affect the cost of bicycle handlebar production, including material selection, the complexity of the manufacturing process, production volume, and overall quality inspection, testing, and design details. It is recommended to discuss these factors during negotiations with the manufacturing partner to better understand cost implications.
-
Can the Manufacturer Ensure Quality Consistency?
Quality consistency is crucial for high-quality bicycle handlebars. The final product must undergo long-term stability testing and multiple ASTM tensile tests to ensure functional reliability. Choosing a manufacturer with a strict quality control process will guarantee product reliability and durability, even after shipment. -
Does the Manufacturer Have Relevant Certifications?
To develop innovative, stable, and safe bicycle handlebars, it is advisable to choose a manufacturer with significant experience and industry-recognized certifications. Obtaining international quality certifications, such as ISO 9001, is important to ensure that the final product meets high market standards.
Conclusion
Now that you understand the bicycle handlebar manufacturing process and key considerations, the next step is to choose a reliable manufacturing partner to produce high-quality and stable products for you.
相關文章
Exploring Aluminum Tubes—From Today’s Applications to Tomorrow’s Trends
Aluminum tubes are hollow, open-ended alloy structures—seamless or welded—ranging from tiny capillaries to large diameters. Renowned for corrosion resistance and easy processing, they’re widely used in piping, machinery, construction, automotive, sports, and furniture.
CNC Tube Bending – Anvil Industries’ Precision Technology for Every Aluminum Curve
Aluminum alloy tubes are lightweight, corrosion-resistant, and versatile. CNC tube bending enables precise, diverse designs. Explore key methods, equipment, and terms, and discover how one-stop services balance quality with cost.
The Role of Precision Aluminum Tube Drawing in Cycling: Combining High Hardness with Optimal Lightweight Design
Tube drawing is vital in bicycle manufacturing, enhancing lightweight frames and structural strength. Precision aluminum tube drawing fine-tunes wall thickness for optimal performance and durability. This technology ensures frames are strong, flexible, and light—essential for competitive racing.