In accordance with the personal data protection law implemented by the European Union, we are committed to protecting your personal data and giving you control over it. By clicking "Accept All", you allow us to place cookies to enhance your experience on this website, assist us in analyzing website performance and usage, and enable us to serve related marketing content. You can manage your cookie settings below. Clicking "Confirm" means you agree with the current settings.
CNC Tube Bending – Anvil Industries’ Precision Technology for Every Aluminum Curve
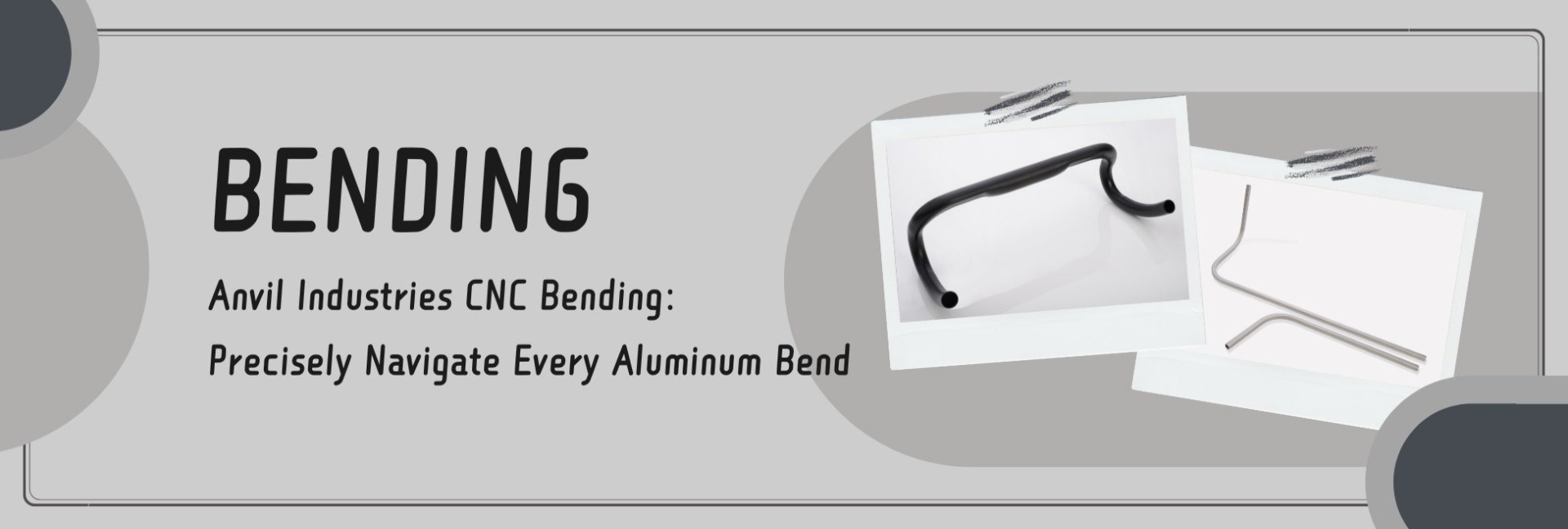
From bicycle and automotive parts to home furnishings and cooling systems, aluminum alloy tubes appear in countless industrial and everyday applications. Their light weight, corrosion resistance, and ease of forming increasingly make them a popular alternative to traditional steel or stainless-steel tubing. However, to achieve complex shapes and high-precision specifications, the innate properties of aluminum alone are insufficient—you also need professional bending and CNC machining to truly unlock their potential.
Through the key points in this article, you can optimize your design and production processes—ensuring that each aluminum tube meets your structural, aesthetic, and efficiency requirements.
Why Do Aluminum Alloy Tubes Need Bending and CNC Machining?
1st: Key Features and Advantages of Aluminum Alloy Tubes
● Lightweight: Aluminum alloy weighs about one-third as much as steel, substantially reducing total product weight.
● Corrosion Resistance: A natural oxide layer defends against most types of corrosion, making it ideal for outdoor or humid environments.
● Superior Thermal Conductivity: Aluminum alloy is excellent for heat exchangers, cooling systems, and other applications requiring efficient heat dissipation.
● Lower Processing Costs: Cutting, drilling, and welding are generally easier with aluminum, helping control overall production costs.
● High Customizability: With the right forming techniques and CNC equipment, you can achieve a wide range of shapes and dimensions.
2nd: Why Use Bending Techniques?
● More Design Options: Relying solely on straight tubes often falls short of aesthetic or functional needs. Bending accommodates arcs and angles suited to tight spaces or unique design requirements.
● Fewer Joints & Welds: Multiple joints amplify stress concentrations and increase corrosion risk. Using a single, continuous bend cuts down on weld points and potential weaknesses.
● Improved Structural Strength & Stability: Properly designed bends help disperse external forces, enhancing overall resilience.
3rd: The Necessity of CNC Machining
● High Precision & Consistency: CNC (Computer Numerical Control) uses programmed instructions to achieve millimeter- or even micrometer-level accuracy, crucial for mass production or high-end industries.
● Multi-Axis Control for Complex Curves: Traditional manual or mechanical bending struggles with intricate 3D shapes. CNC multi-axis benders quickly manage multiple angles and curvatures—shortening development and production timelines.
● Automation & Efficiency: CNC equipment automates multiple procedures, minimizing errors and lowering labor costs.
● Uniform Quality & Traceability: With stringent CNC programming, each product meets the same high standards. Plus, production data is stored for easy monitoring and adjustments later on.
Although aluminum alloy has many natural advantages—lightweight, corrosion-resistant, and versatile—fully leveraging these traits often demands bending and CNC machining. This combination ensures customized, high-strength aluminum tubes with efficient mass-production potential. If you’re seeking top-quality tube bending solutions in Taiwan, prioritize a specialized partner offering both bending expertise and CNC capabilities to integrate every stage from design to final manufacturing, achieving the ideal balance of quality and cost.
CNC Bending Methods & Common Techniques for Aluminum Alloy Tubes
In aluminum tube processing, CNC bending plays a critical role by automating processes and improving precision. Beyond CNC itself, the market offers numerous bending machines and methods. Below are some of the most common techniques:
-
Press Bending
● Overview: A basic method using support dies and a central bending die that applies vertical pressure.
● Advantages: Simple to operate, low-cost equipment, suitable for mid-sized volumes and products without stringent accuracy demands.
● Disadvantages: Less control for thicker or larger-diameter tubes; prone to springback and limited on smaller bending radii. -
Rotary Draw Bending
● Overview: Ideal for high-precision, intricate bends (often with a mandrel to avoid deformation), widely used in bicycle handlebars, medical devices, automotive, and aerospace.
● Advantages: High accuracy, can integrate with CNC, widely adopted in industrial applications.
● Disadvantages: Higher initial equipment costs and a steeper learning curve for proper maintenance and set-up. -
Roll Bending
● Overview: Tubes pass between multiple rollers to gradually shape large-radius bends or continuous curves, such as spiral structures.
● Advantages: Great for large radii or long tubes, allowing continuous bending in the same direction.
● Disadvantages: Not suitable for tight bends or high-precision needs; requires more space and specialized equipment.
Equipment You Need for Effective Tube Bending
Tube Bending Machines
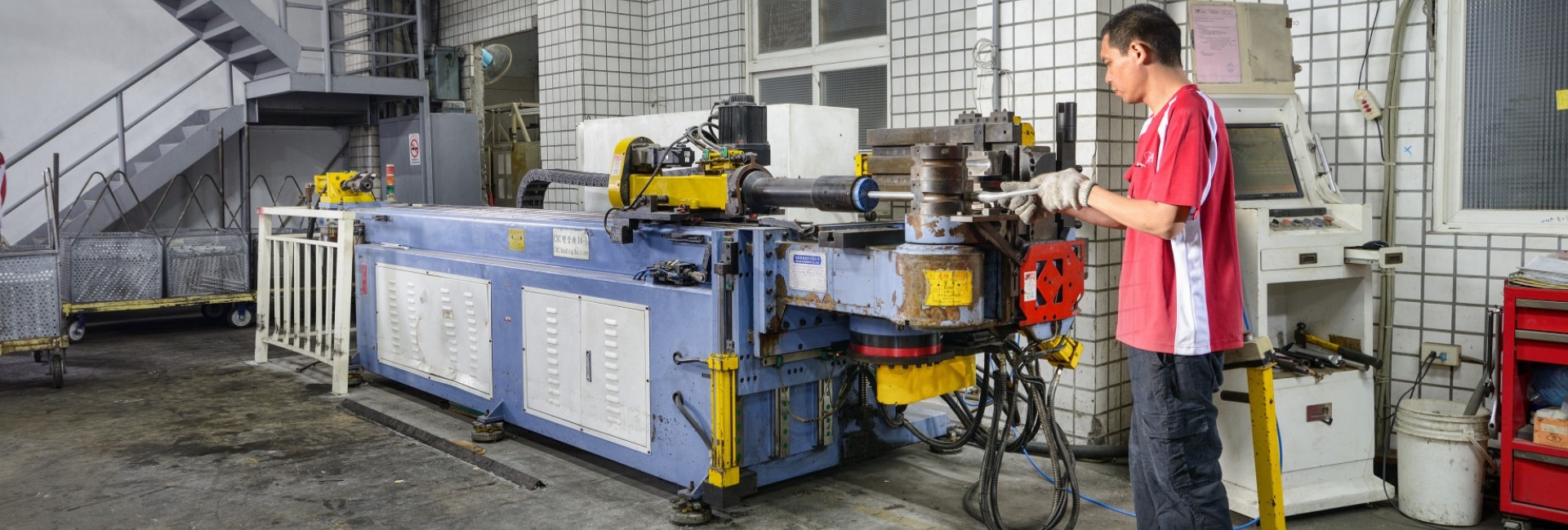
A high-quality bending machine is essential for precision aluminum tube bending.
Anvil Industries operates bending machinery capable of achieving designated bend angles. Other auxiliary equipment further enhances overall quality.
Manu-
Manual Benders
Elec-
Electric Benders
Hydr-
Hydraulic Benders
Dies
Dies (Molds)
Mand-
Mandrel
Wiper
Wiper Die
Common Tube-Bending Terminology
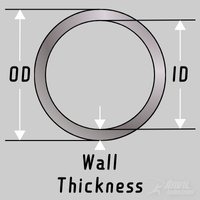
Inside Diameter (ID): Measured from the tube’s inner edge. A mandrel’s size usually corresponds to the ID.
Outside Diameter (OD): Measured from the outer edge; used to determine die sizing for external force application.
-
Degree of Bend (DOB)
The actual angle of the bend, expressed in degrees (°). -
Springback
After releasing the bending clamp, the tube’s elasticity causes minor recoil, slightly reducing the bend angle.
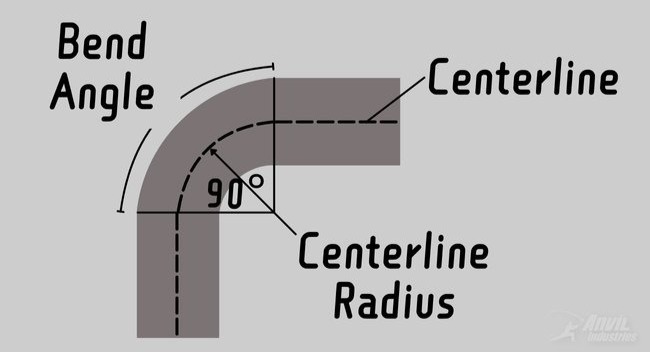
Center Line Radius (CLR)
Is Aluminum Tube Bending Right for Your Product?
Aluminum tubes find extensive use in daily life and industrial applications alike. As modern equipment and processing techniques advance, bending precision continues to improve. With the right materials, techniques, and tools, you can achieve an ideal solution for your custom aluminum tube bends.
Our specialists also offer professional design advice to help you produce tubes that meet your desired specifications with superior quality. Simply send us your design files, and we’ll quickly provide a quote—backed by our unwavering commitment to excellence.
相關文章
Exploring Aluminum Tubes—From Today’s Applications to Tomorrow’s Trends
Aluminum tubes are hollow, open-ended alloy structures—seamless or welded—ranging from tiny capillaries to large diameters. Renowned for corrosion resistance and easy processing, they’re widely used in piping, machinery, construction, automotive, sports, and furniture.
Bicycle Handlebar Manufacturing: Contract, Private Label, & Turnkey Explained – 4 Key Points
Looking for quality bicycle handlebars or starting your own brand? Understanding Contract Manufacturing, Private Label, and Turnkey solutions is essential. This article outlines these models, their processes, and offers tips for choosing the best manufacturing partner.
The Role of Precision Aluminum Tube Drawing in Cycling: Combining High Hardness with Optimal Lightweight Design
Tube drawing is vital in bicycle manufacturing, enhancing lightweight frames and structural strength. Precision aluminum tube drawing fine-tunes wall thickness for optimal performance and durability. This technology ensures frames are strong, flexible, and light—essential for competitive racing.