In accordance with the personal data protection law implemented by the European Union, we are committed to protecting your personal data and giving you control over it. By clicking "Accept All", you allow us to place cookies to enhance your experience on this website, assist us in analyzing website performance and usage, and enable us to serve related marketing content. You can manage your cookie settings below. Clicking "Confirm" means you agree with the current settings.
Heat Treatment in Aluminum Alloys: Influencing Properties and Fundamental Principles
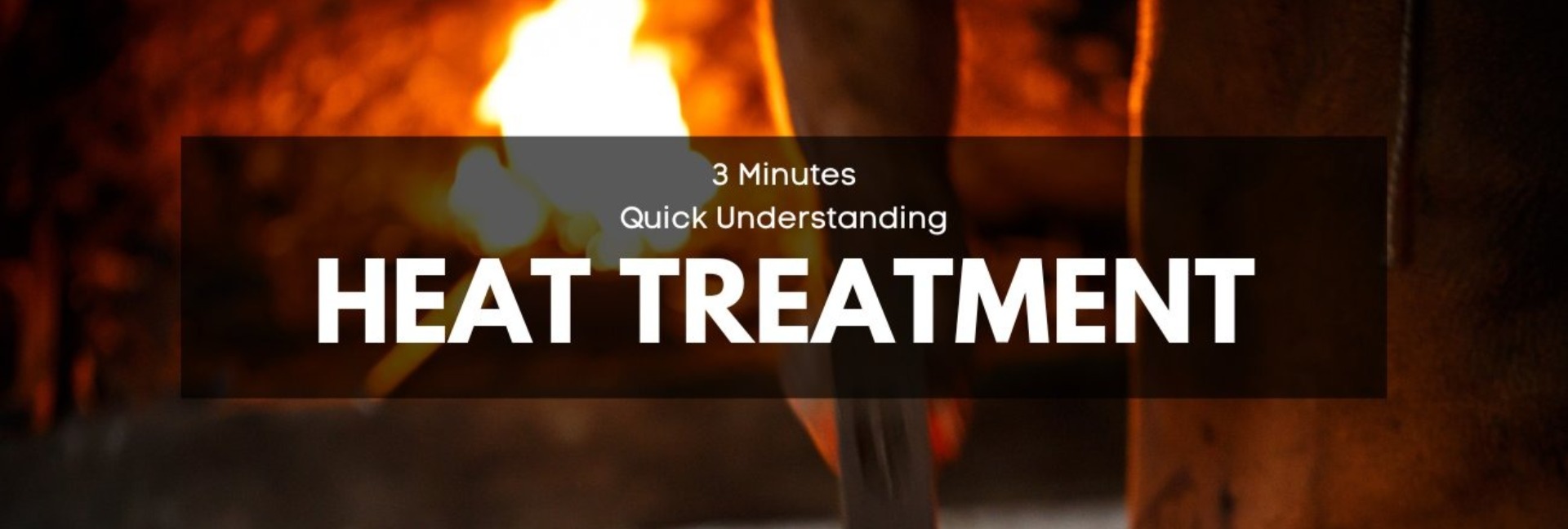
Table of Contents
- What is Heat Treatment? - Understanding the Basic Concept
- Basic Principles of Heat Treatment
- Microstructure Rearrangement
- Solution and Precipitation
- Strain Relief
- Carbon Migration
- Methods and Applications of Heat Treatment
- Annealing
- Normalising
- Quenching
- Tempering
- How Heat Treatment Affects the Properties of Aluminum Alloys
- Common Tempering Codes for Aluminum Alloys
- Conclusion
What is Heat Treatment? - Understanding the Basic Concept
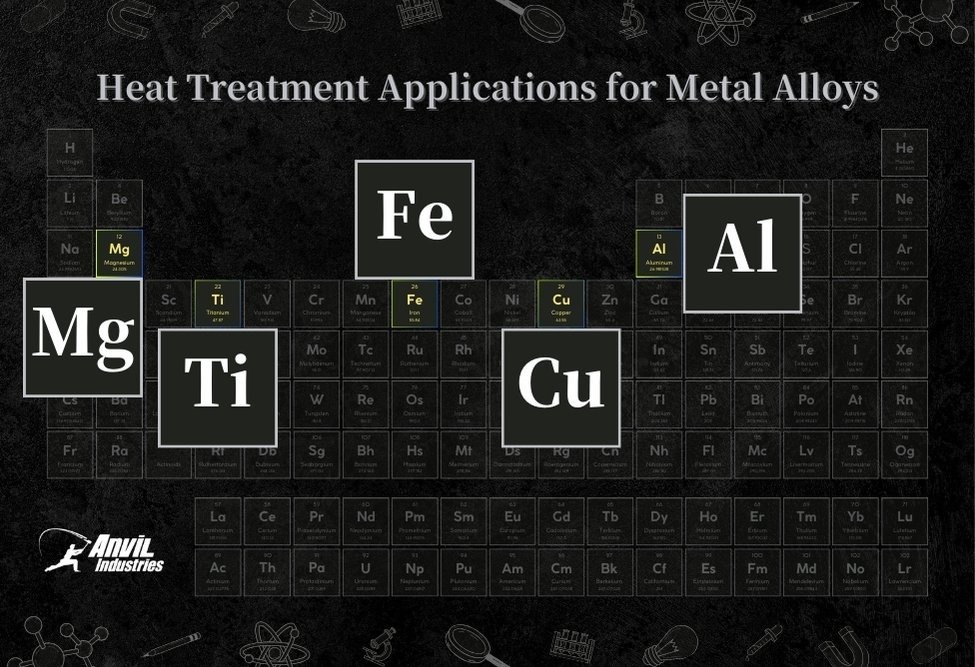
<Heat Treatment Applications for Metal Alloys>
●What is Heat Treatment?
-Heat treatment is an ancient metalworking technique critical for modifying and improving material properties. By heating metals or alloys to a specific temperature, holding them there for a certain period, and then cooling them at a controlled rate, this process changes their structure and properties. For aluminum alloys, it enhances attributes such as hardness, toughness, and wear resistance.
●Can Aluminum Alloys Be Heated?
-Yes. Aluminum alloys, composed of aluminum and other elements, boast benefits like light weight, high strength, good electrical and thermal conductivity, and excellent machinability. Heat treatment can improve the properties of aluminum alloys. Common heat treatment methods for aluminum alloys include annealing, solution treatment, and aging treatment.
●Annealing
-Annealing involves heating aluminum alloys to a specified temperature followed by natural cooling or controlled cooling. This process eliminates internal stresses generated during processing, improving plasticity and toughness. Annealing is widely used in aluminum alloy production and can be categorized into full annealing, partial annealing, and stress relief annealing depending on the specific goals of the processed products.
●Solution Treatment
-Solution treatment heats aluminum alloys above their solubility temperature and then cools them at an appropriate rate. This process dissolves the secondary phases into the solid solution, enhancing strength and hardness.
●Aging Treatment
-Aging treatment involves maintaining aluminum alloys at a specific temperature after solution treatment, then cooling at an appropriate rate. This process precipitates the secondary phases, further increasing strength and hardness.
Through the heat treatment of aluminum alloys, their properties are improved, broadening their range of applications.
Basic Principles of Heat Treatment
Heat treatment fundamentally uses thermal energy to alter the microstructure of metals or alloys, thereby adjusting their mechanical and physical properties. Here's a detailed explanation of the basic principles of heat treatment:
1. Microstructure Rearrangement:
When metals or alloys are heated to a certain temperature, their internal grain structures begin to change. For example, small grains may merge into larger grains or form entirely new phase structures. This reorganization of grains directly impacts the material's hardness, toughness, and other mechanical properties.
2. Dissolution and Solidification:
In solution treatment, one component of the alloy completely dissolves into another component upon heating. Upon cooling, these components solidify in a new way, forming a different microstructure and thus altering the material's properties.
3. Strain Relief:
Processing of metals may introduce internal strains. Through heat treatment, these internal strains can be released, reducing internal stresses and improving overall performance.
Heat treatment achieves specific microstructural outcomes by controlling the rate of heating and cooling, the duration, and the temperature, thereby obtaining the desired mechanical and physical properties. Each type of metal and alloy, depending on its composition and application, requires a specially designed heat treatment process.
Methods and Applications of Heat Treatment
Specific heat treatment processes can significantly enhance the properties and application value of materials. Below are four main heat treatment methods and their characteristics:
1. Annealing:
Annealing primarily softens aluminum parts, adjusts their crystalline structure, eliminates internal stress, and optimizes cold rolling and machining characteristics. Depending on specific needs and applications, annealing can be subdivided into full annealing, partial annealing, stress relieving, among others.
2. T4:
Solution treatment involves heating the workpiece to the optimal temperature for the material and application. After maintaining the required temperature for a set duration, the workpiece is rapidly quenched in water within five seconds to achieve a stable hardness level.
3. T6:
T6 treatment involves artificial aging hardening following solution heat treatment to achieve a higher state of hardness..
4. Aging Treatment:
After solution treatment, the workpiece is aged to a stable state. Mechanical properties vary with product requirements, commonly designated by codes such as T73, T76, etc..
<Practical Operation of Anvil Industries Heat Treatment Furnace>
How Heat Treatment Affects the Properties of Aluminum Alloys
Heat treatment significantly impacts the properties of aluminum alloys, notably increasing their hardness and strength. During specific heat treatment processes, such as age hardening, fine precipitates form in aluminum alloys. These precipitates hinder grain sliding, thus enhancing the material's resistance to deformation.
Furthermore, heat treatments like solution treatment optimize the grain structure of aluminum alloys, enhancing their toughness. After heat treatment, aluminum alloys not only become stronger but also more capable of withstanding external forces without fracturing, making the material easier to process and shape.
Heat treatment also enhances the corrosion resistance of aluminum alloys. When subjected to specific heat treatment processes, their microstructure becomes more uniform, offering better protection against localized corrosion due to structural inconsistencies.
Additionally, the weldability of aluminum alloys can be improved through heat treatment. Proper heat treatment ensures a stronger, more durable structure post-welding. Internal stress generation is a common issue when processing aluminum alloys. Heat treatments like annealing help eliminate these internal stresses, reducing the risk of deformation or cracking during use or further processing. Heat treatment not only improves the mechanical properties of aluminum alloys but also optimizes their microstructure, making them more suitable for diverse applications. This is why heat treatment plays such a crucial role in the production and processing of aluminum alloys.
Common Tempering Codes for Aluminum Alloys
Common heat treatment states like T6, T4, and O each represent distinct heat treatment processes and material characteristics.
T3
T3
Applicable to products that undergo cold working or straightening after solution heat treatment to enhance strength.
T4
T4
Applicable to products that undergo solution heat treatment and do not undergo further cold working (can be straightened or leveled without affecting mechanical performance limits).
T5
T5
High-temperature treatment→Cooling→Artificial aging hardening
Applicable to products subjected to high-temperature forming and then cooled, without subsequent cold working (can be straightened or leveled without affecting mechanical performance limits), followed by artificial aging.
T6
T6
Solution treatment→Artificial aging hardening
Applicable to products that undergo solution heat treatment and do not undergo further cold working (can be straightened or leveled without affecting mechanical performance limits).
T7
T7
Solution treatment→Overaging treatment to a stable state
Different temper designations are used to represent different mechanical properties, commonly used temper designations include T76, T73, etc.
Applicable to products that undergo solution heat treatment and, in artificial aging, the strength exceeds the peak point on the aging curve to achieve certain critical properties.
T8
T8
Solution treatment→Cold working→Artificial aging hardening
Applicable to products that undergo cold working or straightening, resulting in enhanced strength.
T9
T9
Solution treatment→Artificial aging hardening→Cold working
Applicable to products that undergo cold working to enhance strength.
T10
T10
High-temperature treatment→Cooling→Cold working→Artificial aging hardening
Applicable to products that undergo cold working, straightening, or leveling after high-temperature treatment to enhance strength.
Conclusion
Anvil Industries Offers T4, T6, T7 Heat Treatments
If you have any further questions or needs regarding our heat treatment services, please feel free to contact our technical team. Anvil Industries is committed to providing the most advanced and professional solutions, ensuring the highest standard of quality for your projects. We look forward to collaborating with you.
相關文章
Exploring Aluminum Tubes—From Today’s Applications to Tomorrow’s Trends
Aluminum tubes are hollow, open-ended alloy structures—seamless or welded—ranging from tiny capillaries to large diameters. Renowned for corrosion resistance and easy processing, they’re widely used in piping, machinery, construction, automotive, sports, and furniture.
CNC Tube Bending – Anvil Industries’ Precision Technology for Every Aluminum Curve
Aluminum alloy tubes are lightweight, corrosion-resistant, and versatile. CNC tube bending enables precise, diverse designs. Explore key methods, equipment, and terms, and discover how one-stop services balance quality with cost.
Bicycle Handlebar Manufacturing: Contract, Private Label, & Turnkey Explained – 4 Key Points
Looking for quality bicycle handlebars or starting your own brand? Understanding Contract Manufacturing, Private Label, and Turnkey solutions is essential. This article outlines these models, their processes, and offers tips for choosing the best manufacturing partner.