In accordance with the personal data protection law implemented by the European Union, we are committed to protecting your personal data and giving you control over it. By clicking "Accept All", you allow us to place cookies to enhance your experience on this website, assist us in analyzing website performance and usage, and enable us to serve related marketing content. You can manage your cookie settings below. Clicking "Confirm" means you agree with the current settings.
The Role of Precision Aluminum Tube Drawing in Cycling: Combining High Hardness with Optimal Lightweight Design
Table of Contents
- Introduction to Tube Drawing Processes
- Innovations in Aluminum Tube Drawing Techniques
- Distinctive Features of Taiwan's Cycling Industry
- Future Trends – The Rise of Integrated Handlebars?
- Conclusion
Introduction to Tube Drawing Processes
Tube drawing has long been a key manufacturing technique in the bicycle industry, primarily aimed at reducing material weight while enhancing density and strength.
For instance, if a client requires an outer diameter (OD) of Ø31.8 mm with a wall thickness ranging from 1.5 mm to 2.0 mm, the starting material might have an OD of Ø34.9 mm with a wall thickness of 3.0 mm or 3.5 mm. After the tube drawing process, the final product will have the desired OD of Ø31.8 mm and a double butted wall thickness of 1.5 mm to 2.0 mm. This process achieves the specified dimensions while effectively increasing strength and reducing weight.
<Through tube drawing, the process enhances strength and reduces weight with varied wall thickness>
This not only makes the tube material lighter but also increases its strength. The tube drawing process often involves multiple operations, especially when manufacturing high-performance bicycle frames, where multiple tube drawing steps may be required to achieve specific wall thicknesses at different parts. Beyond the basic tube drawing process, several advanced techniques can be applied to precisely shape these materials. These include double-ended tube drawing, tube tapering, or double butted techniques, utilizing different mandrels for each task. This technology allows for the adjustment of wall thickness at various points along the tube as needed, meeting specific customization requirements. It provides an efficient way to precisely control the structure and weight of the product, ensuring that the final product remains lightweight yet performs excellently, particularly vital for products requiring light and strong materials.
Innovations in Aluminum Tube Drawing Techniques
<The Impact of the Rise of Mountain Biking>
Since the 1980s, as mountain biking surged in popularity, the market demanded a technology that not only lightens bicycle frames but also maintains their durability. Early aluminum frames, while lighter, needed thicker walls to match the strength of steel, paradoxically increasing weight and possibly diminishing ride comfort. By 1988, engineers from well-known bicycle brands conducted extensive research on aluminum tubing and discovered that various parts of the bicycle frame experience differing stress levels. For instance, the center of the handlebar and the joint to the upright tube bear less stress, while the grip areas endure more. Based on these findings, they devised a design strategy that increases wall thickness where strength is critical and decreases it where less is required, achieving an optimal balance between strength and weight.
This innovative approach led to the development of tube drawing technology, now extensively applied in mid-to-high-end aluminum and steel frames. This technique adjusts the wall thickness of tubing at various points through drawing or compressing, ranging from single to multiple butted tubes. This not only offers a more precise analysis of stress but also reduces weight while ensuring necessary strength, profoundly enhancing the performance and durability of bicycle frames.
Aluminum tube drawing technology extends far beyond merely enhancing structural design of bicycle frames; it encompasses every detail from selecting raw materials to final processing. The choice of suitable aluminum alloy is crucial in the production of bicycle tubing, as different alloys exhibit distinct physical properties that dictate the quality and performance of the finished product. For instance, 6061 aluminum alloy, known for its lightweight and durable characteristics, is extensively used in manufacturing frames that require a high stiffness-to-weight ratio.
The processing techniques for aluminum tubing are equally vital. Common methods include double and triple wall thickness applications. Double wall thickness entails thicker walls at both ends of the tube and a thinner midsection, providing better flexibility and shock absorption. Triple wall thickness involves thickening the walls at stress points while using thinner walls where less pressure is exerted, thus reducing overall weight. This design enhances the structural integrity and overall performance of the frame. During production, these aluminum frames undergo heat treatment, typically involving T6-level heating followed by rapid cooling, which helps stabilize the internal structure of the aluminum. A subsequent low-temperature process further increases the frame’s rigidity and strength, ensuring excellent performance under various riding conditions. These precise manufacturing techniques and material choices not only showcase innovations in lightweight bicycle frames but also significantly enhance overall riding performance and durability, propelling technological advancements in the cycling industry.
Distinctive Features of Taiwan's Cycling Industry
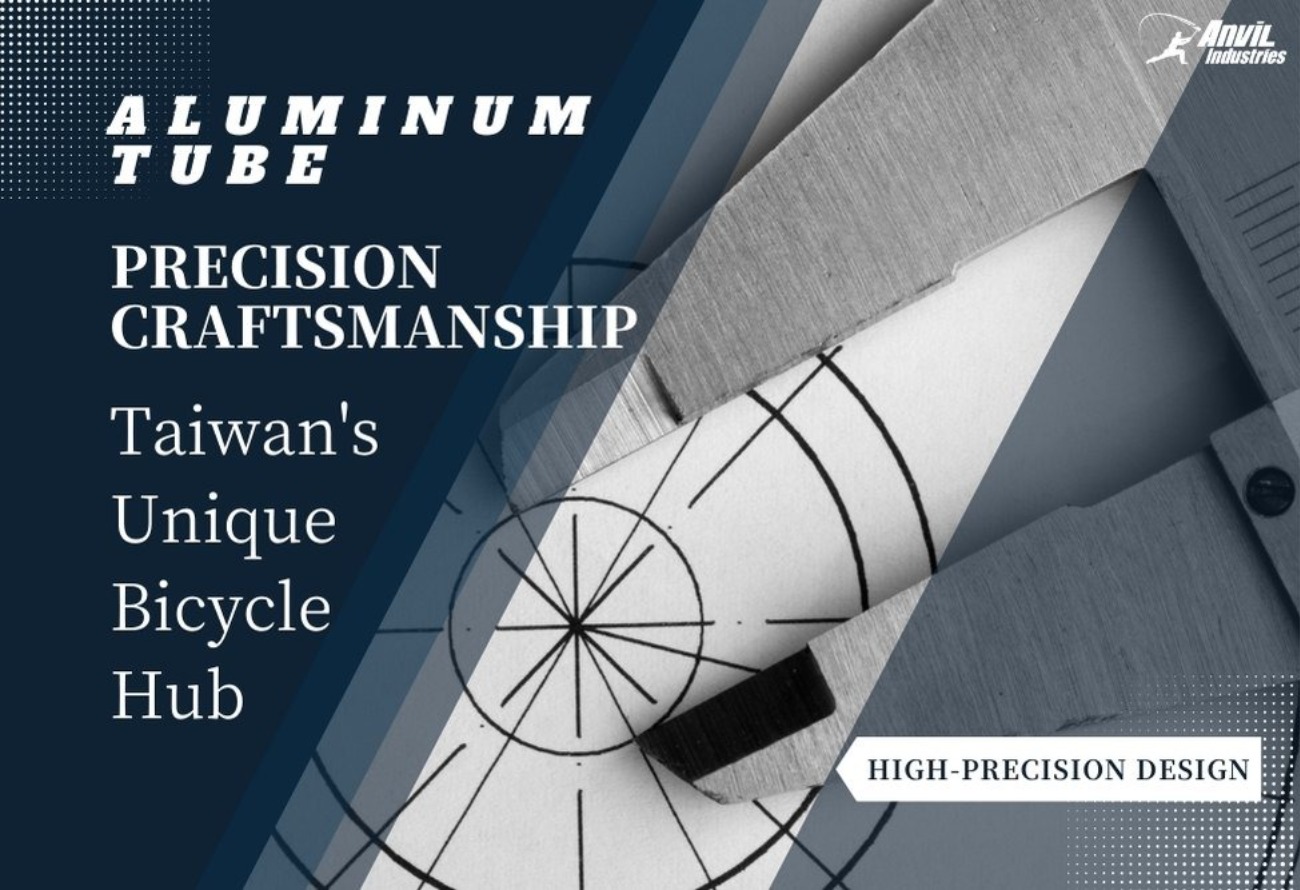
<Precision Specialization in Taiwan's Bicycle Industry>
Within a 70-kilometer radius, Taiwan hosts nearly a thousand bicycle manufacturers, creating a dense supply network characterized by both competition and cooperation. This unique structure is a key driver of innovation in Taiwan's cycling technology. The Taiwanese bicycle industry is renowned for its specialized and segmented manufacturing processes, distinct from traditional whole-bike assembly, featuring a clear division of labor. In this industry, no single manufacturer produces an entire bicycle; instead, numerous specialized small and medium-sized enterprises collaborate, each producing different bicycle components that are assembled into complete products.
Future Trends – The Rise of Integrated Handlebars?
As bicycle technology advances and cycling culture evolves, the market has seen numerous innovative designs emerge, among which integrated handlebars have become a significant trend in the bicycle industry. Known for merging handlebars and the stem into one seamless unit, integrated handlebars offer enhanced rigidity and aesthetic appeal over traditional separate handlebars and stems, gaining increasing favor among professional cyclists and cycling enthusiasts.
Conclusion
Boost Your Bicycle Products with Professional Tube Drawing! Click here to learn more about our advanced precision drawn aluminum tubing technology and submit your inquiry form today. Let us help you elevate your product!
相關文章
Exploring Aluminum Tubes—From Today’s Applications to Tomorrow’s Trends
Aluminum tubes are hollow, open-ended alloy structures—seamless or welded—ranging from tiny capillaries to large diameters. Renowned for corrosion resistance and easy processing, they’re widely used in piping, machinery, construction, automotive, sports, and furniture.
CNC Tube Bending – Anvil Industries’ Precision Technology for Every Aluminum Curve
Aluminum alloy tubes are lightweight, corrosion-resistant, and versatile. CNC tube bending enables precise, diverse designs. Explore key methods, equipment, and terms, and discover how one-stop services balance quality with cost.
Bicycle Handlebar Manufacturing: Contract, Private Label, & Turnkey Explained – 4 Key Points
Looking for quality bicycle handlebars or starting your own brand? Understanding Contract Manufacturing, Private Label, and Turnkey solutions is essential. This article outlines these models, their processes, and offers tips for choosing the best manufacturing partner.